Responsible partners:
Pilot #1 solves unsteady fluid-flow-related shape optimization problems. It uses Computational Fluid Dynamics (CFD) methods and software to design bodies (such as turbomachinery blades, aircraft wings, car components, etc.) which perform optimally during time-varying phenomena. The application in pilot #1 is related to the design of hydraulic turbine and pump-turbine blade rows. Responsible partners in this pilot are NTUA-Copt from the School of Mechanical Engineering and ANDRITZ, one of the global market leaders in the hydropower business. Dr. Evgenia Kontoleontos, Research Engineer at the Research and Development Group of ANDRITZ HYDRO GmbH in Linz, Austria told us more about this pilot.
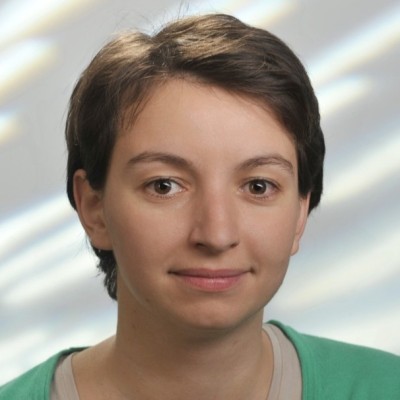
Can you please summarize what pilot #1 is about?
In the last decades, the international market competition, associated to the technical evolution, drove the hydraulic turbine development to produce more compact designs, with smaller and faster machines than in the past. The current demand for energy and grid regulation services led the energy producers to extend the machine operating range, pushing the turbines to operate on conditions that were not experienced in the past. Hydraulic turbomachines are nowadays operated in a far more dynamic way and the flexibility of modern power plants leads to an operation of the equipment in off-design conditions for a larger percentage of time. Under these conditions, several dynamic phenomena such as the pressure pulsations in the fluid flow through the turbine, which were not clearly noticeable in the past, became decisive for the smooth and safe operation of modern hydraulic power plants. As a consequence, the importance of fluctuating loads increases and the unsteady operational behaviour receives more attention from hydraulic component manufacturers.
It is important to focus on the research on these transient phenomena such as the pressure pulsations in the fluid flow through the turbine and its impact on the mechanical structure in order to assure a reliable, smooth, and safe operation of the hydraulic machines. To do so, in the hydraulic industry, the design of hydraulic components with regards to pressure pulsations and unsteady phenomena is mainly based on unsteady CFD calculations that have to be verified with model testing data. The lack of an automatic design optimization for such an HPC application increases the time of manual design and measurement costs in order to come up with the optimal design.
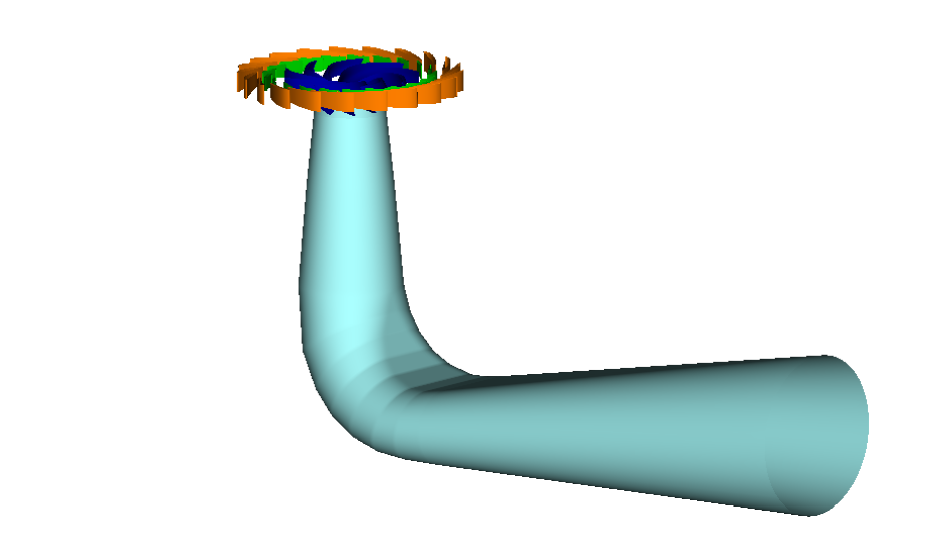
Figure 1: The hydraulic pump-turbine to be optimized in Pilot 1 consists of 21 stay vanes (orange), 21 guide vanes (green), 9 runner blades (blue) and the draft tube (ice blue).
Our objectives within REGALE are:
· to develop a more efficient/resilient/less power consuming automatic unsteady optimization method that will be used on Andritz Hydro HPC hydraulic applications.
· to integrate the unsteady optimization method, that will be developed by NTUA, within ANDRITZ Hydro in-house optimization workflow and to use it for the hydraulic design of pump turbine machines for R&D and commercial projects w.r.t minimization of pressure pulsations.
· to reduce the computational time needed for the design so that the designers will be able to investigate better these unsteady phenomena and prevent any kind of pulsations in the fluid flow, instead of relying only on laboratory testing, which is costly and time consuming.
· to manufacture and validate at ANDRITZ Hydro’s hydraulic laboratory the optimized hydraulic designs for further analysis in order to evaluate the developed method.
· Furthermore, to generalize the results of REGALE to other application domains (e.g. aerodynamic designs) and provide a stepping stone for more complex HPC applications of industrial multi-disciplinary design/optimization (e.g. in the area of aerostructural optimization, aeroacoustics etc.).
What is the research field?
The target sector is Renewable Energy Sources. The research field is focused on hydraulic turbines and especially on the unsteady phenomena, i.e. pressure pulsations that may appear on pump turbine machines, that are installed on pump storage plants, which receive high attention on the global and European hydropower market nowadays.
What are the main challenges in your pilot?
Until now, the steady adjoint-based optimization method is used in almost all design-optimization activities by industries. The necessary methods and software for unsteady applications are available, but the industrial usage of unsteady optimization is extremely limited to small scale problems. It is quite common to replace it with lower cost steady computations and optimizations, which, however, depending on the application, provide lower fidelity results.
If we want to perform an unsteady design optimization evaluating for each time step and each optimization loop these transient phenomena, such as the pressure pulsations in the fluid flow through the whole turbine, a powerful computational platform should be available and, also, storage requirements and efficient I/O should be guaranteed. Therefore, this HPC application of unsteady design optimization on hydraulic turbines, given the practical limitations (throughput, storage, cost of I/O), poses a series of challenges for a resource manager, as the one that will be developed in REGALE.
At the same time, we can also say that the high computational cost (compared to steady state approaches) can be an obstacle during the development of the method.
It is, in fact, a real HPC application of great industrial interest, with very intensive I/O operations, which are spread among the bulk of the computational effort.
It is, in fact, a real HPC application of great industrial interest, with very intensive I/O operations, which are spread among the bulk of the computational effort. Hence, the nature of the application promotes the role of the resource manager, that will be investigated in REGALE, to one of vital importance for the successful and efficient completion of the overall computational task and provides a challenging proving ground for next-generation beyond the state-of-the-art resource management systems.
What do you expect from REGALE?
The main outcome of the pilot has high priority for ANDRITZ Hydro. We expect to integrate the unsteady optimization method, that will be developed by NTUA, within our in-house optimization workflow, in order to use it for the hydraulic design of pump turbine machines for R&D and commercial projects with regards to minimization of pressure pulsations.
By reducing the computational time needed for the design, our designers will be able to achieve in less time the optimal design and predict better these unsteady phenomena. At the same time the computational results of this method will be validated with the laboratory measurements.