Responsible partners:

The aim of pilot #5 is to achieve optimum material designs, while taking into account uncertainties. Dr. Ioannis Kalogeris, Postdoc in Computational Mechanics at National Technical University of Athens gave us some deeper insight.
Can you please summarize what pilot #5 is about?
Developing polymeric materials with superior mechanical and damping properties is of great interest to many industrial sectors, including construction, automotive, aerospace and energy industries. Polymer materials, although light materials, are flexible and relatively low-strength materials, with respect to other competitive materials like steel. It is therefore necessary to add high-strength and stiffness fillers in order to improve their mechanical properties. The rapidly advancing innovations on carbon-based nanomaterials such as graphene and carbon nanotubes allow producing materials with extraordinary mechanical properties, making them ideal inclusions for reinforced composites. One important application of these carbon-based composites is in the design of automotive parts, which are required to be lightweight, durable and have high strength.
In the context of the Regale project, our aim is to design high-performance automotive parts comprised of carbon reinforced polymers with optimal material configuration. Our research will target specifically the design of a car bumper, which is a component where light weight in combination with high strength and large ductility-work hardening behavior is pursued. Figure 1 depicts the geometry of such a part, which is reinforced at a microstructural level with CNTs. Finding the optimal weight fraction of the CNTs in the host material and their orientation at different locations of the bumper, so as to increase its crash-worthiness, will be the goal within the Regale project.
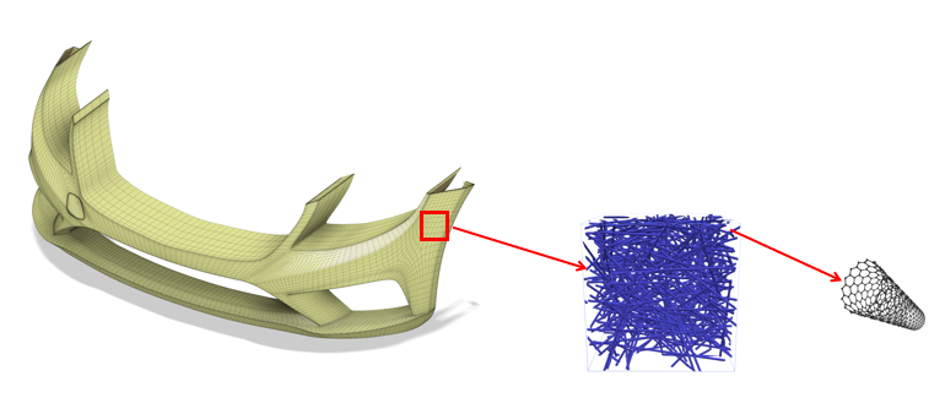
Figure 1: Car bumper made up of CNT-reinforced polymer
What is the research field?
The research fields involved in this endeavor are material analysis and design, multiscale finite element methods, uncertainty quantification, and stochastic optimization.
What are the main challenges in your pilot?
Polymers reinforced with carbon nanomaterials are highly heterogeneous materials at a microstructural level due to the existence of the nano-sized inclusions. In order to produce an accurate numerical model that will allow us to capture the composite’s mechanical behavior, we need to resort to the so-called multiscale finite element method, which allows us study the problem at multiple scales, ranging from the nano-scale of the carbon nanomaterials to the macro-scale of the car bumper comprised of the composite polymer.
“the most sensible approach to solve this otherwise intractable problem is by taking full advantage of modern HPC capabilities.”
Despite its high accuracy though, this method is associated with immense computational requirements. Additionally, in order to achieve optimum material designs we need to perform a stochastic optimization analysis, which requires millions of model evaluations for various material configurations. Given the current technological advancements, the most sensible approach to solve this otherwise intractable problem is by taking full advantage of modern HPC capabilities that will enable us to simultaneously perform massive numbers of simulations.
What do you expect from REGALE?
Within the REGALE project, we aim to develop a comprehensive, numerically efficient and scalable workflow for material design that would take into account multiscale uncertainty. The proposed HPC-enabled computational framework is expected to push the barriers of current technological capabilities further and deliver a new paradigm for material analysis and design. The applications of this pilot should not be limited to the study of automotive parts, but also reach other fields of industrial interest, such as aerospace, heat transfer applications, electrical conduction etc.